Nowadays the LED screens are everywhere. We could see them in the airport, shopping mall, roadside, etc. If you are planning to install a screen near the sea coast, there are some important points you should know:
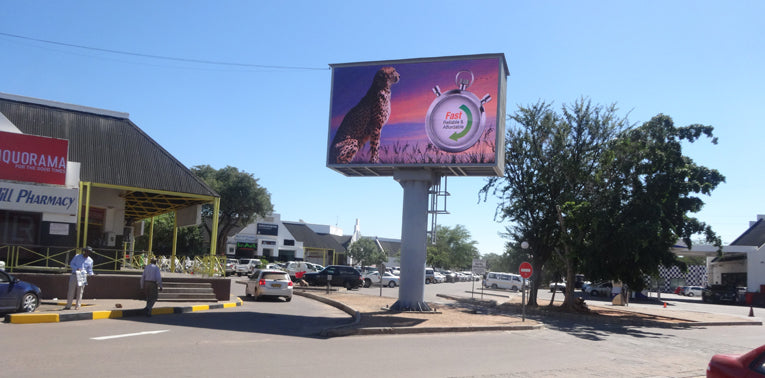
Why sea coast installation is different from other places? The seashore area has very strong UV light, which would affect the lifespan of the LED. Meanwhile, the humidity is very high, and more importantly, the air is salty. The salty air would have huge effect on the LED’s lifetime.
How to make a good LED screen by the sea? What kinds of material should be used?
If the distance between the screen and the sea is within 100m, DIP LED should be used. There are two types of outdoor LEDs: DIP LED and SMD LED. They are used different kind of materials and encapsulation ways. Please view the below pictures.
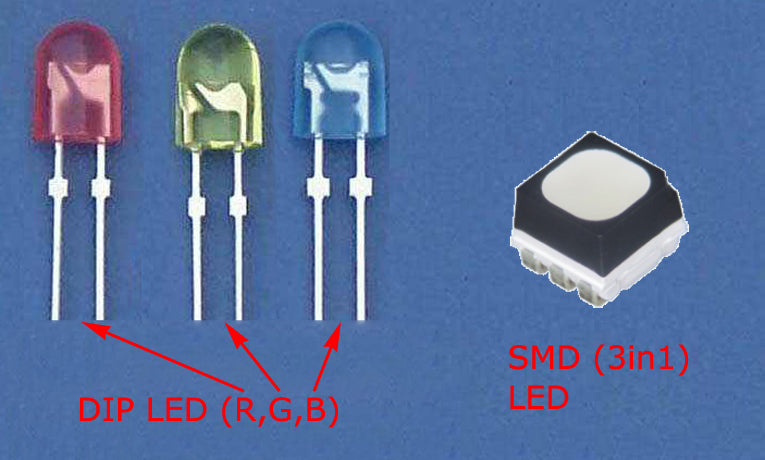
As you could see DIP LED is has stronger IP level because its whole body is wrapped by a same material, while the body of SMD LED is made of two different kinds of material. The DIP LED works in strong UV light and salty air environment better than SMD LED does. Although SMD has better color uniformity and viewing angle than DIP LED, stable performance means everything. If the screen is very close to the sea, DIP LED would be a better option.
If the distance between the screen and the sea is more than 100m, SMD LED is also fine. But the LED quality must be good. No matter how far is your screen away from the sea and whether is DIP LED or SMD LED you want to use, it is always wise to use high quality LED. High quality LED should be encapsulated with gold bonding wire, see the below image for the LED encapsulation image.
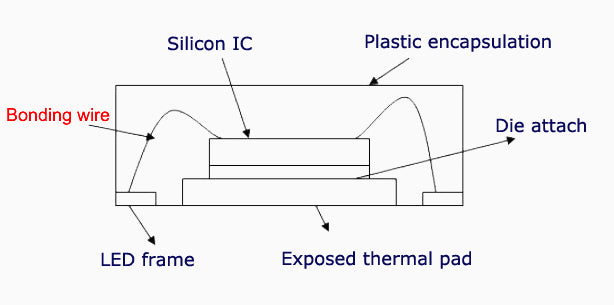
There are several types of bonding wire material for the LED encapsulation. One is gold material, there are others like copper material or even iron material. The LED with gold bonding wire encapsulation is much more reliable than the other types of LED. It has high level of anti-corrosion and antioxidant. It also could stand higher temperature, and the thermal shock which was caused by the temperature difference during daytime and nighttime.
When the screen is installed on the sea coast, the salty air and strong UV light would have strong impact on the LED. The other material like copper or iron bonding wire couldn’t stand that. And after few months, many these kinds of LED would die. That is why we need to use the LED with gold bonding wire encapsulation.
The back of the LED modules should be sealed. When the salty air goes inside the cabinet, it will corrode the electron components on the back of the module, such as driving IC, resistance, etc. We could put some coating on the back of the module so that the electron components would be isolated from the salty air.
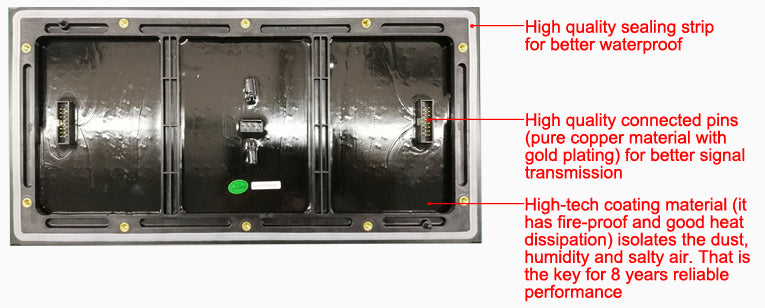
The cabinet needs aluminum material so that the it will not get rusted. Meanwhile, the cabinet should not leave the ventilations so that the salty air will not go inside to corrode the power supply, cables, receiving card, etc.

What’s more, the screen should use high quality power supply. The power supply should have CE certificate with PFC function. This type of power supply will be very reliable and they don’t generate much heat. Additionally, the power supply has no fans, so the power supply will not be affected by the humidity which makes it more reliable. Meanwell brand HSP model power supply is a good option.